At Trustbridge, our Design for Manufacturability (DFM) services help you avoid expensive surprises and unnecessary delays by optimizing your part designs for the real-world constraints of production — before a single tool is cut or part is made.
Whether you're prototyping a new product, preparing for injection molding, or trying to reduce cost in an existing design, our engineers provide detailed, actionable feedback to align your design intent with the realities of machining, molding, casting, printing, and more.
We’ve supported hundreds of successful product launches across industries — and we’ve seen what works, what fails, and what costs you time and money. Let us bring that insight to your design process.
Design for Manufacturability (DFM) Services: Optimizing Product Design For Efficient Manufacturing
Our DFM Services at a Glance
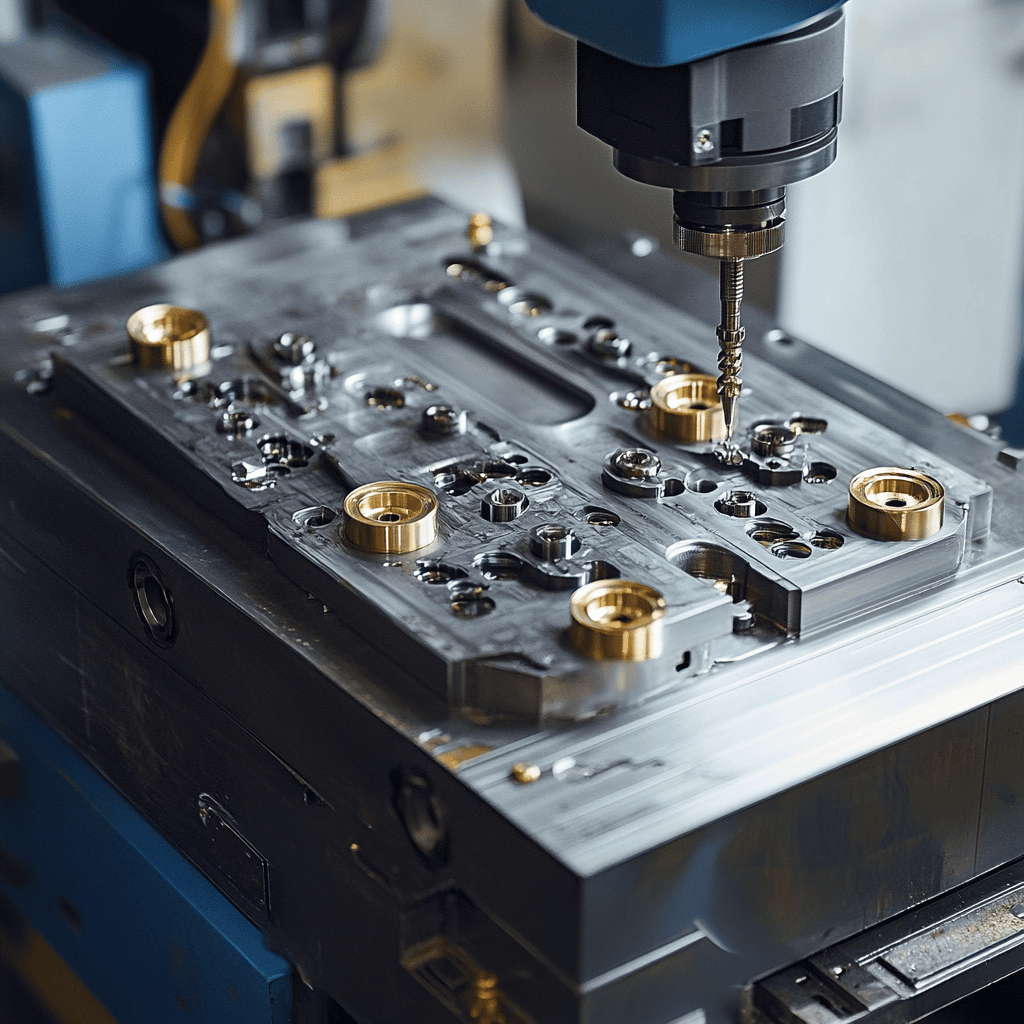
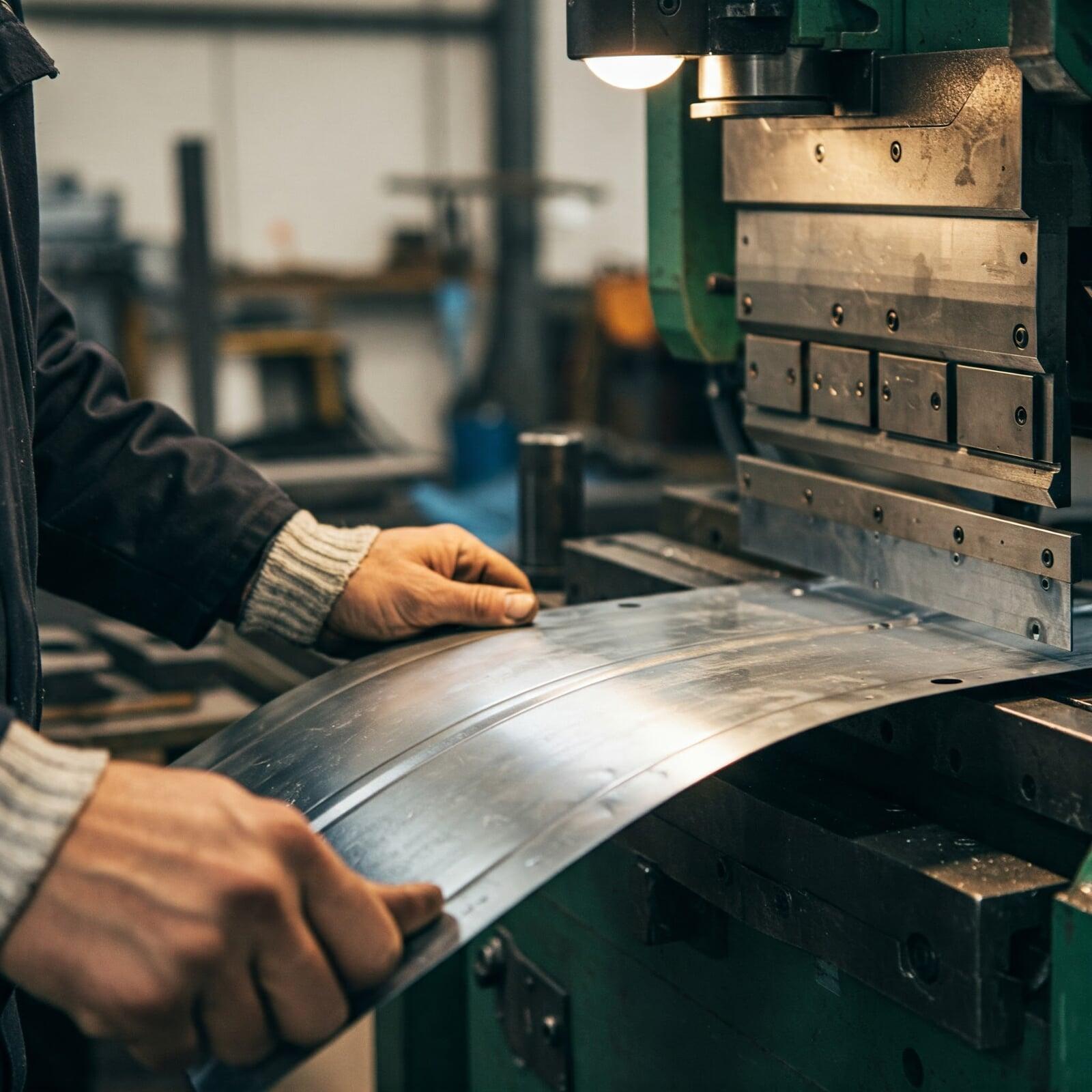
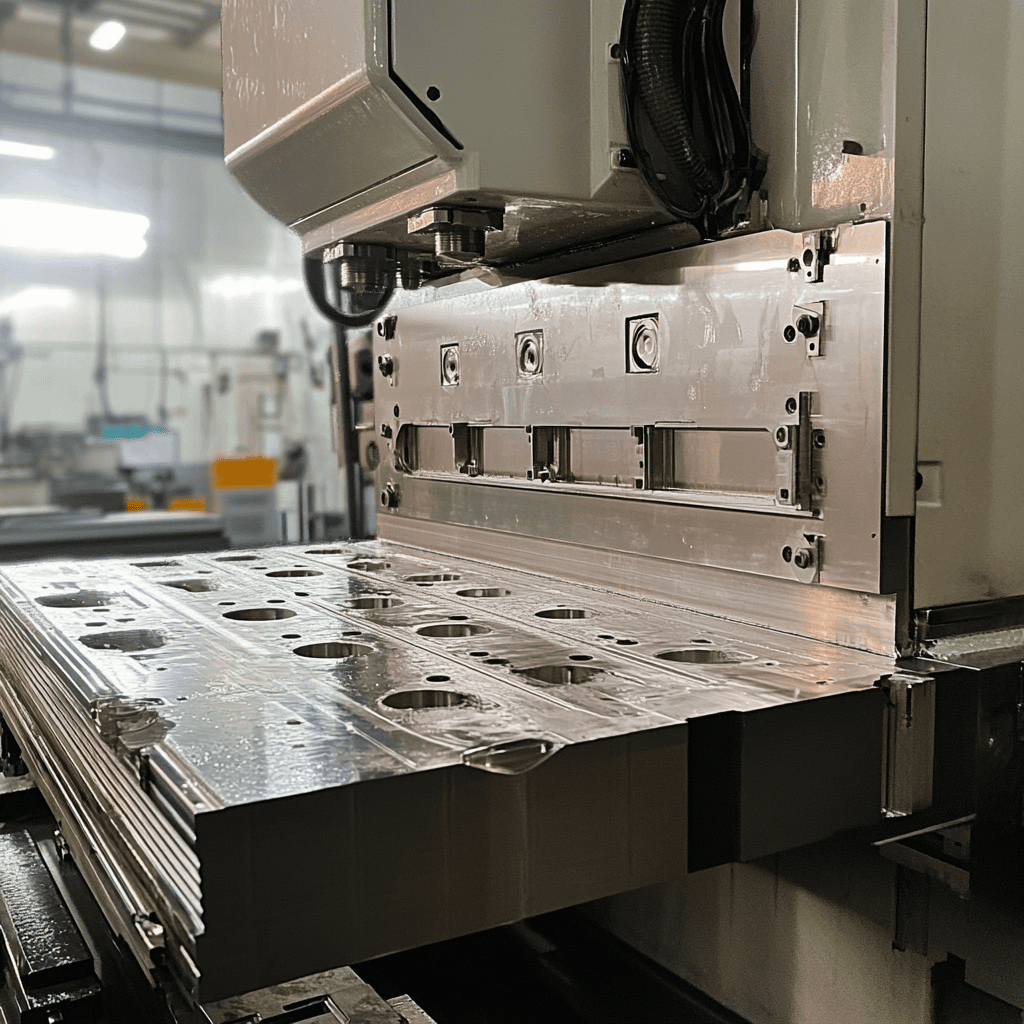
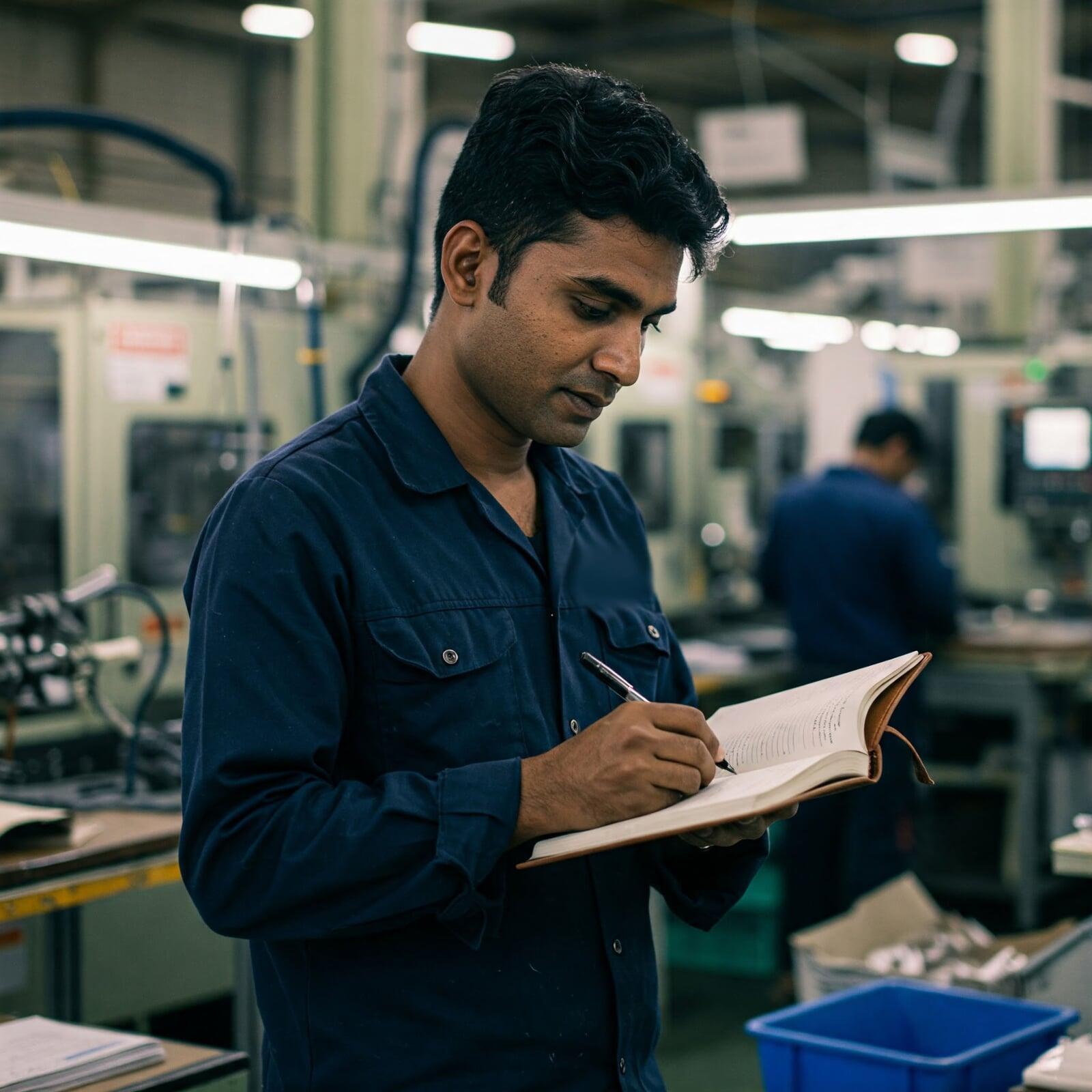
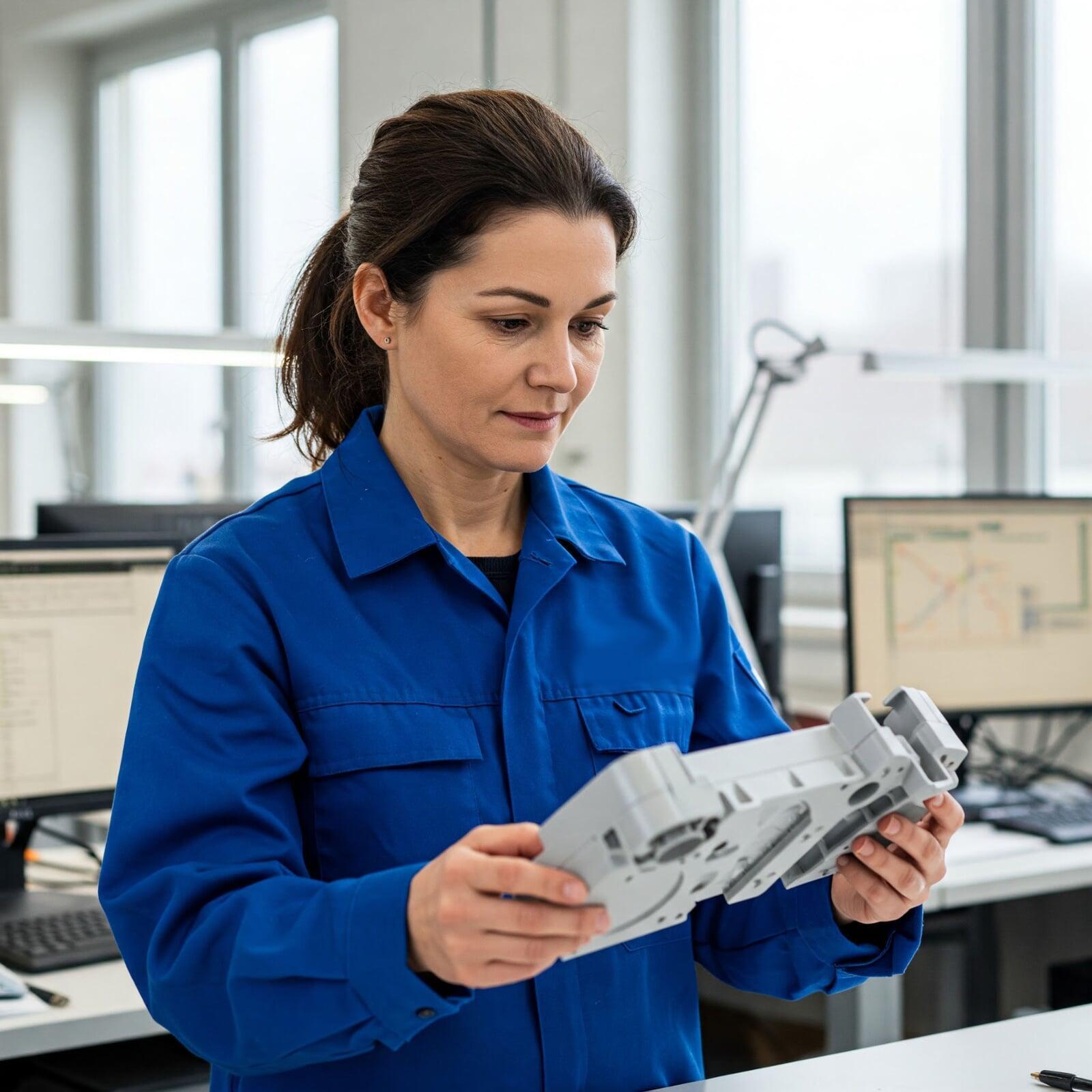
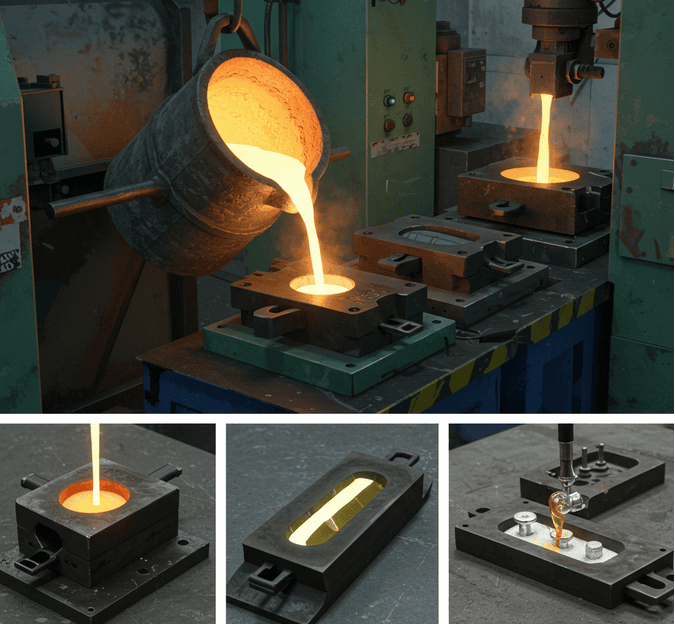
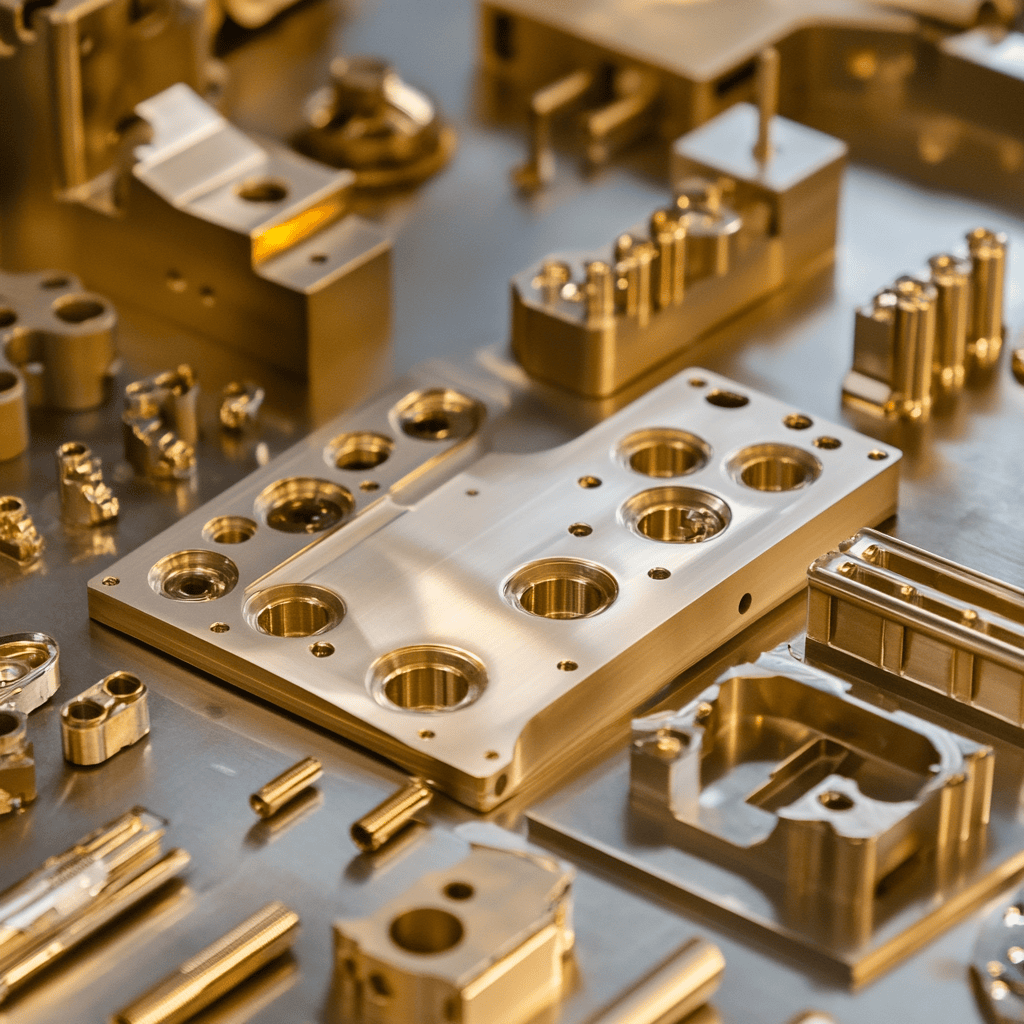
Don’t Wait to Find Out What Went Wrong. Design It Right the First Time.
Our DFM reviews start at the earliest stages of development — and can save you weeks and thousands of dollars down the line.
Explore Related Services
3D Printing
Rapid, cost-effective prototyping and low-volume production with complex geometries and minimal tooling.
Sheet Metal Fabrication
Cut, bend, and assemble custom enclosures, brackets, and panels — scalable from prototypes to full production runs.
Injection Molding
High-volume plastic part production with consistent quality, fast cycle times, and low per-unit cost once tooled.