Bridging the Gap Between Design and Manufacturing
Bridging the Gap Between Design and Manufacturing
Introduction
For engineers and designers, transforming innovative concepts into manufacturable products is a critical process that requires both precision and collaboration. Bridging the gap between design and manufacturing can help you reduce costs, streamline production, and enhance product quality. Achieving this alignment is not just about improving technical processes—it’s about fostering teamwork, leveraging technology, and understanding the nuances of both design and production. In this blog, we’ll explore in-depth strategies to align your design goals with manufacturing realities, ensuring seamless collaboration and successful project outcomes.
Understanding the Challenges
Design and manufacturing often operate in silos, leading to disconnects that can cause inefficiencies, delays, and costly redesigns. By delving deeper into these challenges, we can better understand how to overcome them:
Unrealistic tolerances: Overly tight tolerances can increase manufacturing complexity and costs. Designers may not always understand the trade-offs between precision and feasibility.
Material mismatch: Designers may select materials without considering machinability, availability, or cost, leading to production delays or higher expenses.
Complex geometries: Features that are difficult to machine or fabricate can slow down production and increase costs, especially when alternative approaches are overlooked.
Inadequate communication: Misalignment between design teams and manufacturing partners can result in errors, misunderstandings, and wasted resources.
Evolving project scopes: Late-stage design changes without considering manufacturing implications can lead to significant inefficiencies and rework.
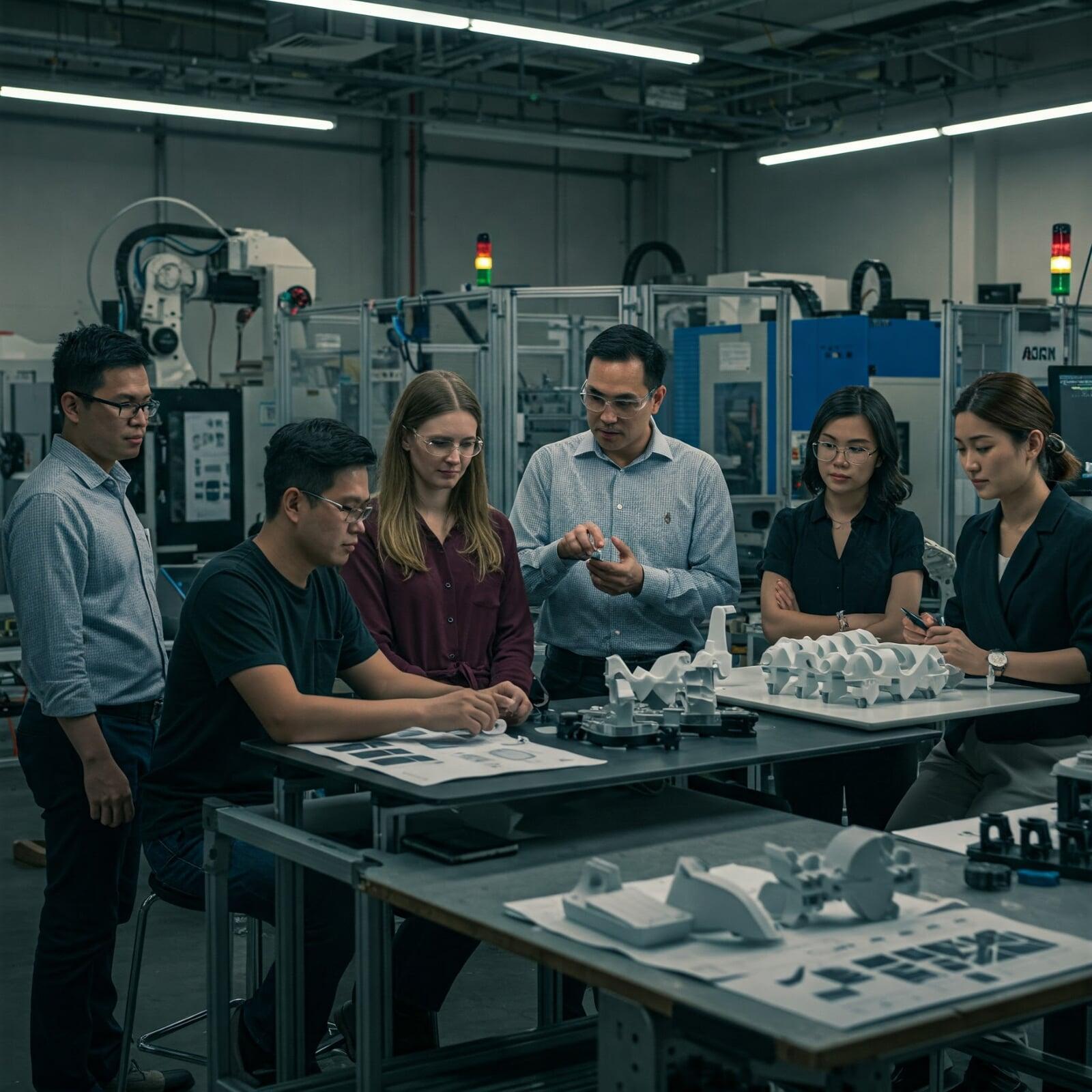
Best Practices for Bridging the Gap
1. Collaborate Early and Often
Involve manufacturing teams during the design phase to gather input on feasibility, costs, and lead times. Early collaboration minimizes the risk of design revisions and ensures alignment with production capabilities. For example:
Hold joint workshops where design and manufacturing teams discuss goals and constraints.
Incorporate real-time feedback loops into the design process using shared digital platforms.
2. Design for Manufacturability (DFM)
Applying DFM principles ensures that your designs are both practical and cost-effective. Here are some advanced strategies:
Simplify part geometries to reduce machining steps while maintaining functionality.
Use modular design approaches to create interchangeable parts that streamline production.
Reduce the number of custom components in favor of standard, off-the-shelf parts to lower costs and lead times.
3. Leverage CAD/CAM Tools
Advanced CAD/CAM software is a game-changer for integrating design and manufacturing. By simulating machining processes, you can identify potential issues, optimize designs, and ensure compatibility with specific production methods. For instance:
Use tolerance analysis tools to balance precision with manufacturability.
Simulate material removal processes to predict machining times and tool wear.
Explore generative design options to find innovative solutions that minimize waste.
4. Standardize Material Selection
Choosing the right materials requires a nuanced approach that considers performance, availability, and cost. To achieve this:
Collaborate with suppliers early to understand the trade-offs between strength, durability, and machinability.
Use material selection tools to compare properties and costs across different options.
Create a database of preferred materials tailored to your projects to ensure consistency.
5. Establish Clear Communication Channels
Foster open communication between design and manufacturing teams. This involves:
Using collaborative tools like shared file repositories for real-time updates.
Setting up regular check-ins to address questions, changes, and challenges promptly.
Creating comprehensive documentation, including detailed CAD files and production notes, to minimize ambiguity.
Case Study: Collaborative Design in Action
A mid-sized engineering firm successfully bridged the gap between design and manufacturing by involving machinists in the prototyping stage. By adopting DFM principles and standardizing components, they achieved: a
A 25% reduction in production time.
$50,000 in material cost savings over six months.
Improved relationships between design and production teams, fostering a culture of collaboration.
This case underscores the value of early collaboration and strategic planning in achieving manufacturing excellence.
Conclusion
Bridging the gap between design and manufacturing is essential for engineers and designers seeking to deliver high-quality, cost-effective products. By prioritizing collaboration, applying DFM principles, and leveraging technology, you can align design goals with manufacturing realities, paving the way for success. This alignment not only ensures efficient production but also empowers designers and engineers to innovate confidently, knowing their ideas are achievable and impactful.
Trustbridge is a leading design and manufacturing consultancy and service provider. We specialize in helping creators and companies bring products from conception to mass production. If you’d like to discuss any of the content in this paper or your own specific needs in detail, please Schedule a Consultation with Trustbridge. Accelerate your product’s journey to market with expert guidance. You can read more about our business in the Trustbridge Overview Paper.