Exploring Honda's Integration of Metal Additive Manufacturing in Automotive and Mobility Solutions
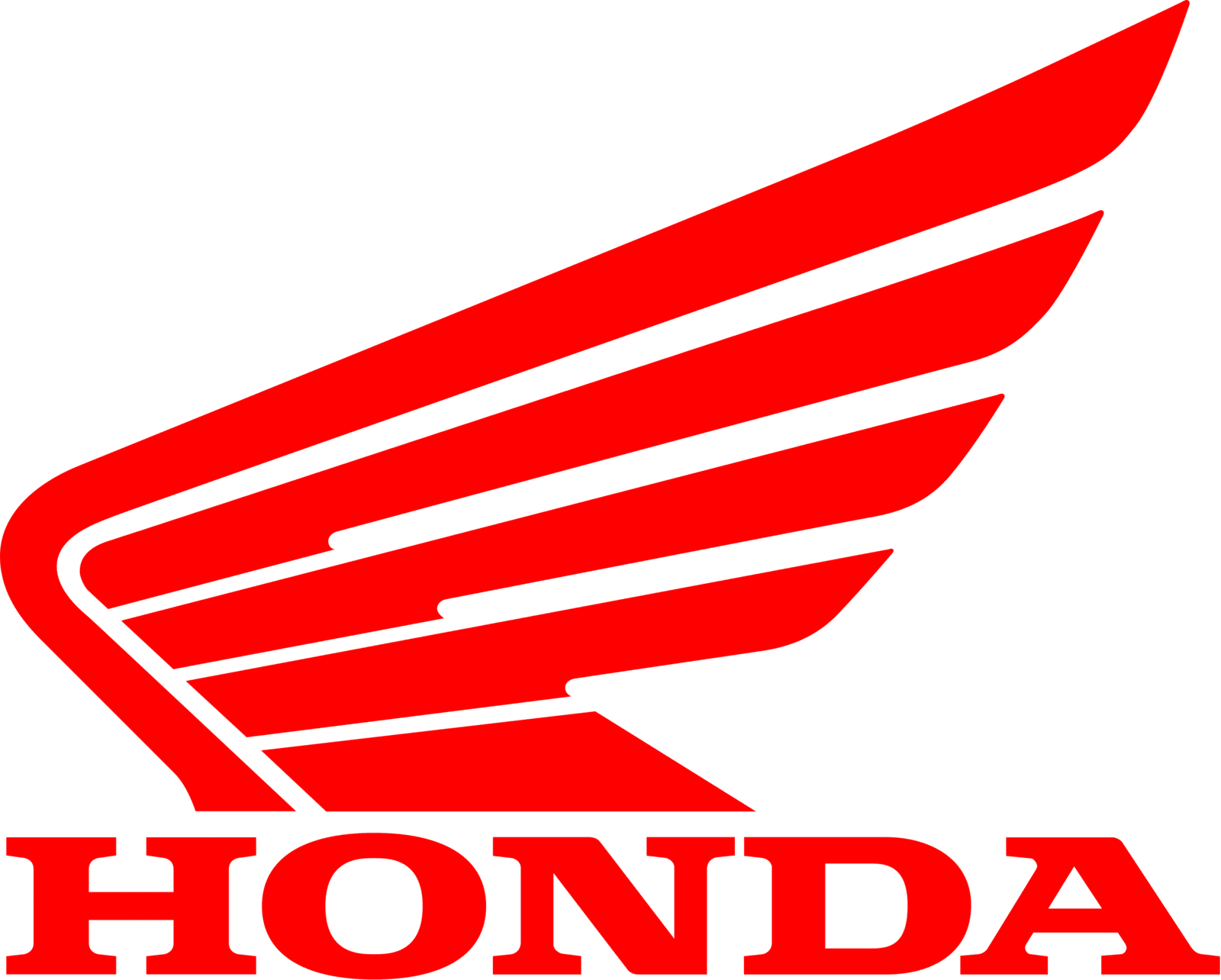
In an industry where speed, performance, and precision are everything, Honda is once again leading from the front—this time with additive manufacturing (AM). The automotive giant has begun integrating metal powder bed fusion (PBF) into its workflow, marking a pivotal moment in how high-performance parts are designed and produced.
At Trustbridge Design, we’re passionate about showcasing not just what’s possible, but how innovations like these can be applied across industries—from motorsport to medical, mobility to manufacturing.
How Honda is Using Metal PBF to Innovate
Honda’s use of metal PBF is not a gimmick—it’s a strategic leap. Known for engineering excellence, Honda is leveraging this cutting-edge 3D printing process to create parts that are lighter, stronger, and more complex than traditional manufacturing would allow.
Two standout examples:
- F1 Power UnitsIn Formula 1, every gram matters. By using metal PBF, Honda engineers are creating engine components that are optimized for strength and weight. The result? Faster lap times, better fuel efficiency, and parts that thrive under extreme thermal and mechanical stress.
- Wheelchair Racer HandlebarsAway from the racetrack but no less competitive, Honda applies AM to custom aluminum handlebars for racing wheelchairs. These parts are tailored to each athlete, offering better ergonomics, aerodynamics, and resilience. That’s performance engineering with a human touch.
Why This Matters for the Industry
Honda’s use of AM is more than a cool headline—it’s a shift in how manufacturing works.
- From Prototypes to ProductionWhat was once reserved for prototyping is now capable of producing end-use, performance-grade parts. Honda is proving it on the track and in the lab.
- Performance, Reimagined3D printing allows for topology-optimized and lattice structures that reduce weight without compromising strength—a game-changer for any mobility application.
- Customization at ScaleWhether for sports, medical, or niche mobility, AM enables a level of personalization that would be cost-prohibitive with traditional methods.
- Supply Chain ResilienceWith in-house AM, companies reduce lead times, cut logistics costs, and can iterate designs rapidly—a competitive edge in any product development cycle.
Where Trustbridge Design Comes In
We believe in not just keeping up with innovation—but making it accessible.
At Trustbridge Design, we work with startups, SMEs, and enterprise clients to bring the benefits of additive and precision manufacturing into their own workflows:
- Advanced CAD + SimulationWe create parts optimized for AM and CNC, using structural and thermal analysis to refine your designs before a single gram of material is used.
- Hybrid Manufacturing ExpertiseFrom SLA to SLS to metal PBF via our partner foundries, we build your prototypes and production parts. Need tight tolerances? Our in-house CNC machining closes the loop.
- Rapid Prototyping to ProductionWhether it’s five iterations in a week or prepping a final part for certification, our team moves fast—and smart.
Designers, Take Note: Lessons from Honda
- Break Free from Traditional LimitsEmbrace the design freedom of AM—think internal channels, lattice cores, and organic forms that weren’t possible before.
- Combine Materials for PerformanceUse AM for critical metal parts, CNC for finish, and composites for the rest—hybridization is the new standard.
- Iterate, Don’t HesitateAM accelerates feedback. Test your ideas in days, not months.
- Design for the End UserHonda’s wheelchair work is a reminder: engineering is about people. Fit, comfort, and user-centric features should always lead.
Let’s Build What’s Next—Together
If this kind of innovation gets you thinking, then let’s talk. At Trustbridge Design, we help:
Automotive startups refine and scale faster.
Mobility innovators make lighter, stronger, smarter parts.
Sports and medical designers push performance and comfort.
From initial sketches to final production, we’re with you every step of the way.
Let’s co-create the future—because the next big thing in mobility starts with a bold idea, and a partner who can bring it to life.