Choosing the Right Materials for CNC Machining: Strength vs. Cost Trade-offs
Choosing the Right Materials for CNC Machining: Strength vs. Cost Trade-offs
Introduction
Selecting the right material for CNC machining is a critical decision that impacts not only the performance of the final product but also its production cost and lead time. Each material offers a unique balance of mechanical properties, such as strength, hardness, and corrosion resistance, as well as varying degrees of machinability and availability. When balancing these considerations, the trade-offs between material performance and cost-effectiveness must be carefully evaluated. Some projects may demand premium materials for strength and durability, while others may prioritize speed and cost, favoring easier-to-machine options.
This white paper provides an in-depth comparative analysis of the most commonly used materials in CNC machining, helping you make informed decisions based on your project’s unique requirements. By understanding the strengths, weaknesses, and cost considerations of each material, you can optimize your designs for both functionality and budget.
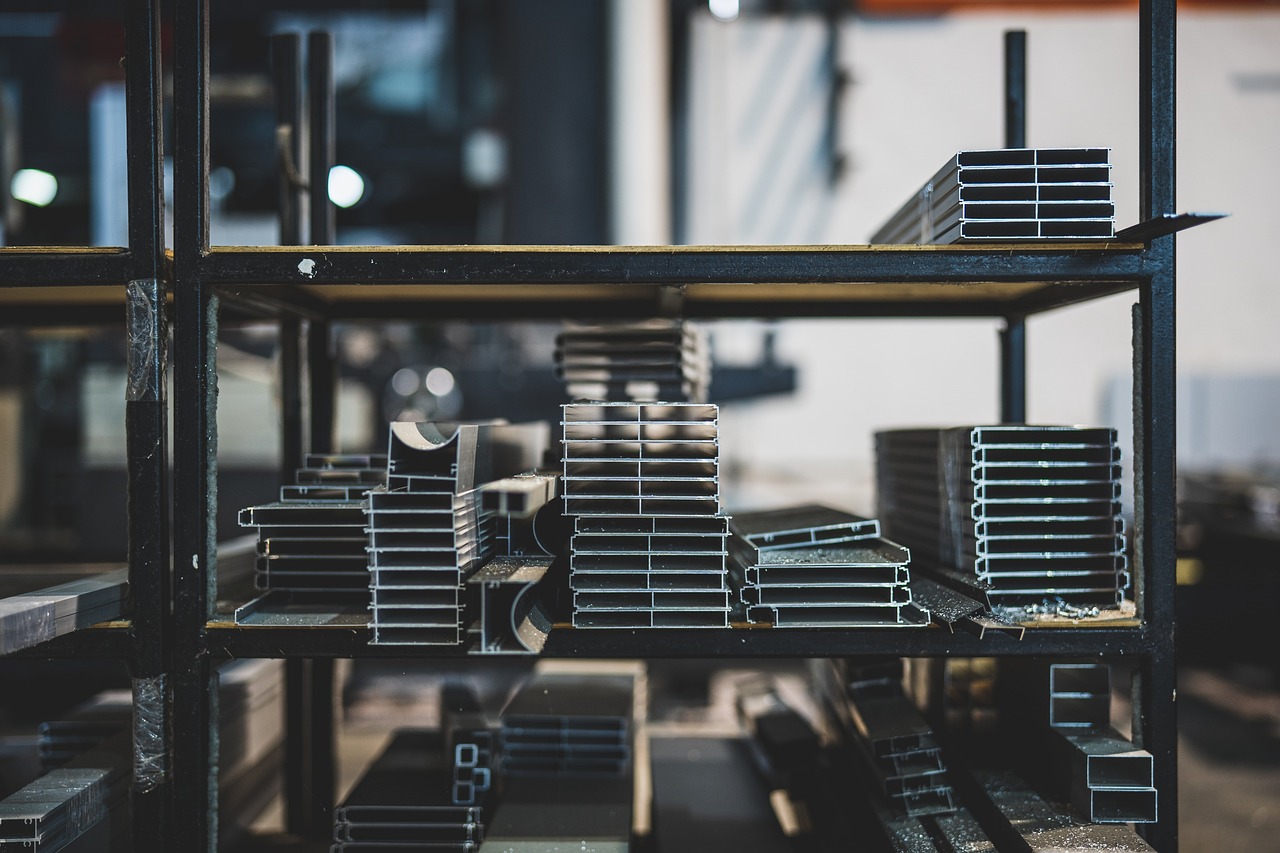
Key Considerations for Material Selection
Material selection should not be based solely on mechanical properties. Several additional factors affect your decision, including:
Cost per unit (based on raw material, machining time, and post-processing)
Machinability (how easily the material can be cut without causing excessive tool wear or requiring specialized processes)
Weight (critical for aerospace and automotive industries)
Corrosion resistance (important for outdoor or chemical-exposed applications)
Thermal conductivity (relevant for heat dissipation in electronics and machinery)
Understanding these factors will help you balance cost and performance during the design phase.
1. Metals for CNC Machining: Strength and Performance
Aluminum Alloys: The Cost-Effective Workhorse
Aluminum is one of the most popular materials for CNC machining due to its high strength-to-weight ratio, corrosion resistance, and excellent machinability. It is commonly used in aerospace, automotive, consumer electronics, and industrial machinery.
Key Grades:
6061 Aluminum: Widely used for its balance of strength, corrosion resistance, and ease of machining.
7075 Aluminum: Significantly stronger and more durable than 6061, but at a higher cost. Ideal for aerospace and structural applications.
5052 Aluminum: Known for its exceptional corrosion resistance, making it ideal for marine and chemical applications.
Cost vs. Strength Trade-off:
Aluminum grades like 6061 are highly cost-effective for general use, while 7075 provides superior strength at a premium price. For non-critical parts, opting for 6061 or even lower-cost aluminum alloys can save significant costs.
Typical Applications:
Prototyping
Lightweight structural components
Enclosures for electronics
Steel Alloys: The Backbone of Industrial Applications
Steel offers superior strength, durability, and wear resistance compared to most other metals. However, it is denser and harder to machine, which increases machining time and tool wear.
Key Grades:
1018 Carbon Steel: A cost-effective low-carbon steel with good machinability and moderate strength.
4140 Alloy Steel: A versatile alloy steel known for its toughness, high strength, and resistance to wear.
304 Stainless Steel: Corrosion-resistant and ideal for parts exposed to moisture or chemicals.
316 Stainless Steel: Superior to 304 in terms of corrosion resistance, often used in marine and medical applications.
Cost vs. Strength Trade-off:
Carbon steels, such as 1018, are more economical than alloy steels or stainless steels. However, alloy steels like 4140 provide much higher tensile strength and are ideal for parts that undergo high stress. Stainless steels are often more expensive but essential for corrosion resistance in harsh environments.
Typical Applications:
Gears, shafts, and industrial machine parts
Medical implants and instruments
High-strength structural supports
Brass and Copper Alloys: High Machinability and Conductivity
Brass and copper are prized for their excellent machinability and conductivity, making them ideal for electrical and fluid handling components. They are soft compared to steel and aluminum, which allows for fast cutting speeds but also limits their strength.
Key Grades:
C360 Brass: The standard for CNC machining due to its superior machinability, corrosion resistance, and attractive appearance.
C110 Copper: Highly conductive and ideal for electrical components, though more expensive and prone to oxidation.
Cost vs. Strength Trade-off:
Brass is more expensive than aluminum but offers faster machining times due to its softness. Copper is typically chosen for its electrical and thermal properties rather than mechanical strength.
Typical Applications:
Electrical connectors and heat exchangers
Fluid fittings and decorative components
Fasteners and precision bearings
Titanium Alloys: Strength at a Premium
Titanium offers exceptional strength-to-weight ratio, corrosion resistance, and biocompatibility, making it a preferred choice in aerospace, medical, and military applications. However, it is difficult to machine, requiring slower speeds and specialized tools.
Key Grades:
Grade 2 Titanium: Pure titanium with excellent corrosion resistance but lower strength. Ideal for chemical processing components.
Grade 5 (Ti-6Al-4V): The most commonly used titanium alloy, offering superior strength and heat resistance.
Cost vs. Strength Trade-off:
Titanium is significantly more expensive than steel and aluminum, both in raw material cost and machining cost. It is typically reserved for parts where high strength and low weight are critical, and there is no room for compromise on durability.
Typical Applications:
Aircraft components
Surgical implants
High-performance automotive parts
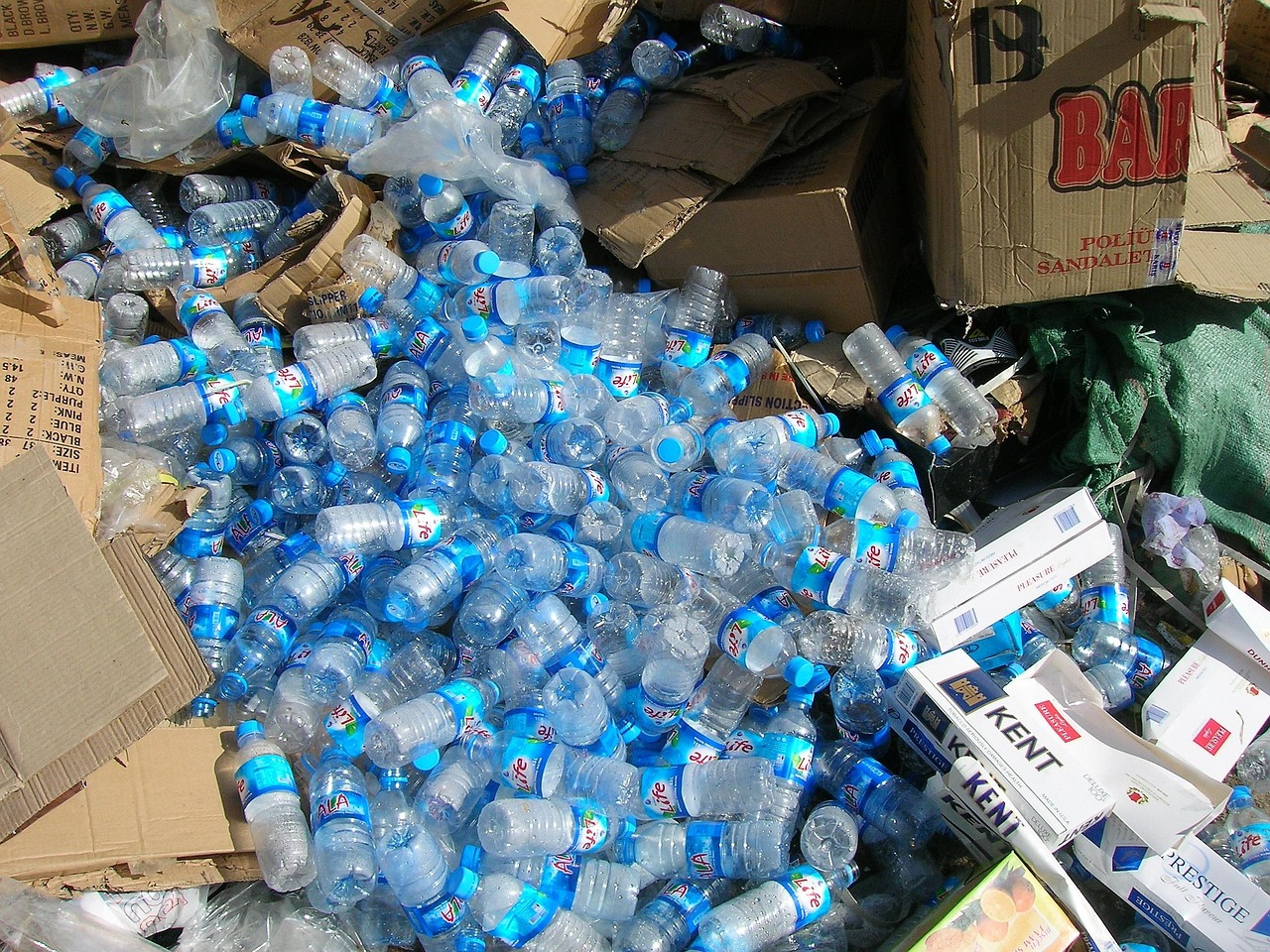
2. Plastics for CNC Machining: Lightweight and Cost-Effective Solutions
Delrin (POM): The Versatile Engineering Plastic
Delrin, a type of acetal plastic, is highly machinable and offers excellent dimensional stability, low friction, and high wear resistance.
Strengths:
Low friction and self-lubricating properties
Excellent for gears, bushings, and housings
Maintains stiffness and shape across a range of temperatures
Cost vs. Strength Trade-off:
Delrin is more expensive than basic plastics like ABS but far more versatile for engineering applications. It is typically more cost-effective than metals for non-load-bearing parts.
Nylon (PA): Tough and Impact Resistant
Nylon is a durable plastic known for its impact resistance, chemical resistance, and flexibility.
Strengths:
High impact resistance and toughness
Excellent resistance to abrasion
Can absorb moisture, which can impact dimensional stability
Cost vs. Strength Trade-off:
Nylon is often used in place of metal for lightweight components that require durability but not extreme precision. However, moisture absorption can cause warping in humid environments, making it unsuitable for some applications.
Polycarbonate (PC): Transparent and Tough
Polycarbonate is known for its transparency, toughness, and heat resistance.
Strengths:
High impact resistance (shatterproof)
Maintains clarity and strength at high temperatures
More durable than acrylic but harder to machine
Cost vs. Strength Trade-off:
Polycarbonate is more expensive than ABS or acrylic but provides far superior impact resistance and heat resistance. It is often used in safety equipment, optical components, and impact-resistant housings.
3. Balancing Cost, Machinability, and Performance
Selecting the right material requires balancing several factors:
If strength and low weight are key concerns: Consider aluminum or titanium.
For parts exposed to extreme conditions: Stainless steel or high-grade alloys may be necessary.
For rapid prototyping or non-load-bearing parts: Plastics like Delrin or ABS offer an affordable solution.
For electrical or thermal conductivity: Copper or brass may be ideal, despite their higher raw material costs.
Conclusion
Choosing the right material for CNC machining involves careful consideration of cost, mechanical properties, and application-specific requirements. While premium materials like titanium and stainless steel offer unparalleled strength and corrosion resistance, they come at a significantly higher cost. Conversely, materials like aluminum, carbon steel, and engineering plastics provide a more cost-effective balance of performance and machinability for many projects. Understanding the trade-offs between strength and cost ensures that your project remains within budget while meeting performance standards.
Trustbridge is a leading design and manufacturing consultancy and service provider. We specialize in helping creators and companies bring products from conception to mass production. If you’d like to discuss any of the content in this paper or your own specific needs in detail, please Schedule a Consultation with Trustbridge. Accelerate your product’s journey to market with expert guidance. You can read more about our business in the Trustbridge Overview Paper.